Ensuring corrosion resistance in stamped auto parts, especially in regions with harsh environmental conditions or exposure to road salt, involves a combination of material selection, surface treatments, and quality control measures. Here are the key steps taken:
Material Selection:
Multi-Criteria Decision Analysis (MCDA): Utilize MCDA methodologies to comprehensively evaluate materials, considering not only mechanical and corrosion properties but also factors like recyclability, weight, and manufacturing feasibility.
Thermodynamic Analysis: Conduct thermodynamic studies to assess the corrosion resistance of materials in varying environmental conditions, ensuring a nuanced understanding of their long-term performance.
Surface Treatments:
Nanotechnology Applications: Explore nanotechnology applications, such as nanostructured coatings and nanocomposite materials, for their potential to enhance surface properties and provide an unparalleled level of protection against corrosion.
Functionalized Coatings: Develop coatings with functionalized additives, such as corrosion-responsive nanoparticles or microcapsules releasing corrosion inhibitors, to actively counteract corrosion at the molecular level.
Corrosion Inhibitors:
Biodegradable Inhibitors: Investigate the use of biodegradable inhibitors derived from renewable sources, aligning with eco-friendly practices and addressing concerns related to the environmental impact of corrosion inhibitors.
Smart Inhibitor Systems: Implement smart inhibitor systems that can autonomously sense corrosion initiation and release inhibitors as needed, creating a self-regulating and adaptive corrosion protection mechanism.
Seam Sealing and Design Considerations:
Topology Optimization: Apply topology optimization techniques to minimize stress concentrations and design auto parts with optimized geometries that inherently resist corrosion.
Additive Manufacturing Integration: Explore the integration of additive manufacturing technologies to produce complex, corrosion-resistant structures with minimal joints, reducing susceptibility to corrosion.
Quality Control and Testing:
Machine Vision with AI: Combine machine vision systems with advanced artificial intelligence algorithms for defect recognition, enabling the detection of subtle irregularities in the stamped auto parts that may indicate potential corrosion vulnerabilities.
Robust Testing Protocols: Develop and adhere to robust testing protocols, including cyclic corrosion testing and electrochemical impedance spectroscopy, to simulate a wide range of environmental conditions and validate the long-term corrosion resistance of auto parts.
Adherence to Industry Standards:
Global Certification Programs: Pursue participation in and certification from globally recognized corrosion standards programs, such as NACE (National Association of Corrosion Engineers) or ASTM International, to demonstrate a commitment to the highest industry benchmarks.
Continuous Improvement Initiatives: Establish a culture of continuous improvement, where regular reviews of industry standards lead to proactive adjustments in manufacturing processes to stay ahead of emerging requirements.
Regular Maintenance and Inspection:
Predictive Maintenance Analytics: Integrate predictive maintenance analytics tools that leverage machine learning algorithms, historical corrosion data, and real-time environmental inputs for precise predictions, ensuring timely and cost-effective maintenance interventions.
Augmented Reality Maintenance Guides: Develop augmented reality maintenance guides for vehicle owners, providing interactive, step-by-step instructions for identifying and addressing corrosion-related issues, fostering a proactive maintenance approach.
Collaboration with Suppliers:
Joint Research Ventures: Engage in joint research ventures with material suppliers, investing in collaborative projects aimed at developing novel materials with unprecedented corrosion resistance properties.
Supply Chain Integration: Optimize supply chain integration by implementing real-time information exchange systems with suppliers, enabling swift response to material quality variations and ensuring a seamless flow of high-quality materials into the manufacturing process.
Auto Parts Electrophoresis Small Size Dust Cover
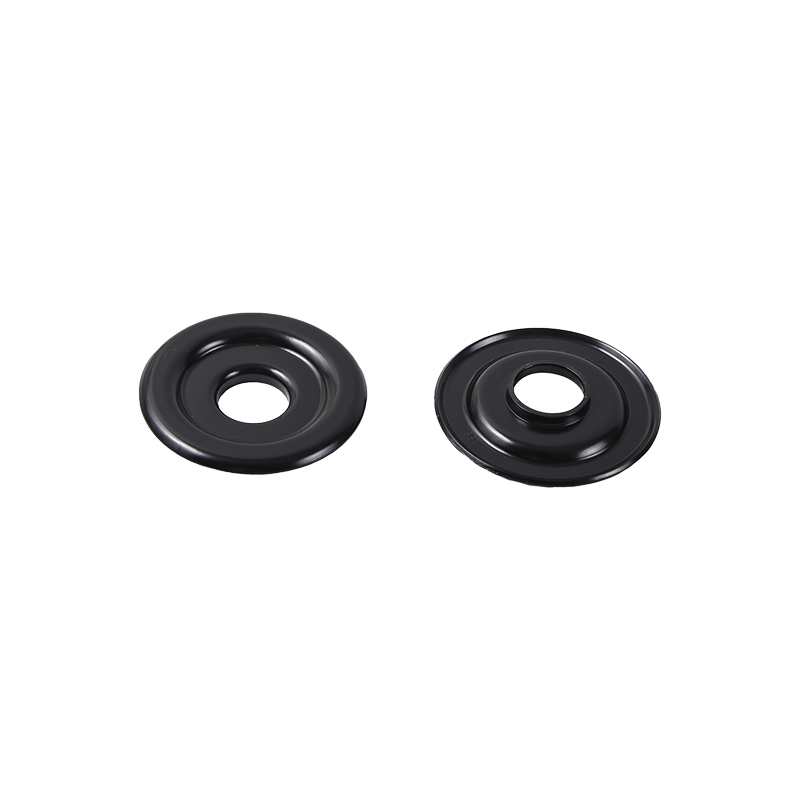
Auto Parts Electrophoresis Small Size Dust Cover
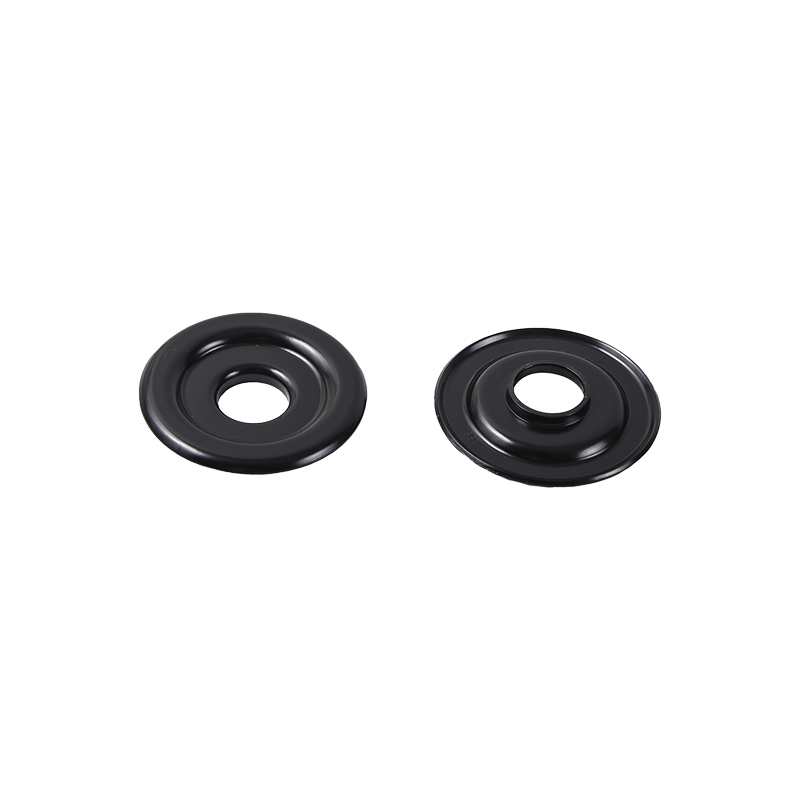